The process of CNC machining entails the use of a computer to manage maker devices for a much more trusted and consistent output. Specialized tools and methods are frequently utilized to enhance the machining procedure, which can consist of making use of cutting tools coated with difficult products to decrease wear and improve efficiency when functioning with soft steels like copper.
Discover copper cnc machining just how copper CNC machining combines innovative modern technology with lasting techniques to generate detailed, high-precision parts, driving technology throughout sectors such as electronic devices, auto, and aerospace.
Amongst the primary benefits of CNC machining copper is the capability to produce intricate forms that standard machining techniques may not accommodate. The repeatability of the CNC machining procedure makes certain that mass manufacturing of copper components preserves uniformity, therefore meeting rigorous sector criteria.
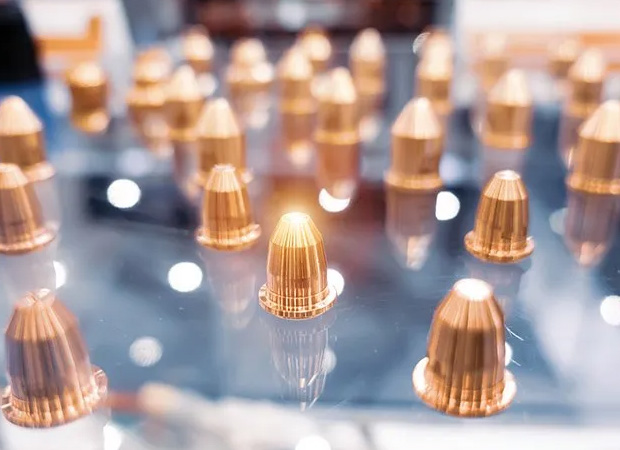
Temperature level monitoring plays a critical function in the CNC machining of copper because of its ability to perform warmth quickly. High-speed machining can result in significant heat generation, which might negatively affect the residential or commercial properties of the copper and exacerbate device wear. CNC machinists frequently turn to innovative air conditioning methods, such as flooding coolant systems and mist lubrication, to handle heat and expand tool life. By regulating the temperature level during machining, suppliers can accomplish better surface area finishes, boost accuracy, and generate components with improved mechanical residential properties. In addition, with the introduction of technologies like high-pressure air conditioning systems and ingenious reducing fluid solutions, CNC machining can accomplish optimal efficiency while effectively taking care of thermal impacts.
The sustainability element of CNC machining copper is not to be forgotten. Copper is a highly recyclable product-- reusing copper requires up to 90Discover countersink size chart just how copper CNC machining combines advanced innovation with lasting practices to create detailed, high-precision components, driving advancement across industries such as electronics, vehicle, and aerospace. less energy than mining and processing brand-new copper ore. CNC machining, coupled with lasting practices, can lower waste by allowing makers to make use of scrap copper from other procedures. The integration of recycling and environment-friendly practices right into machining procedures aligns with the significantly eco-conscious worths of consumers and sectors alike. As companies aim to minimize their carbon impact and improve their environmental stewardship, CNC machining can play a crucial role in assisting in these purposes by supporting recyclable materials flow within the supply chain.
Along with sustainability, cost-effectiveness is one more important variable for suppliers choosing CNC machining for copper components. Though the preliminary financial investment in CNC equipment might be significant, the long-term benefits can outweigh the expenses. CNC machining offers a decrease in labor prices due to its automatic nature and reduces the demand for extensive manual intervention. In addition, the precise control & repeatability provided by CNC modern technology lowers scrap rates, lowering material expenses. In addition, for small to medium batch production runs, CNC machining can verify extra economical compared to conventional machining processes, as it enables seamless adjustments and style modifications without comprehensive retooling. This capability to pivot swiftly can be helpful, especially in hectic markets where market needs can move suddenly.
As technology evolves, the capabilities within CNC systems are broadening, further boosting the capacities of copper machining. These simulations allow better preparation of tool paths and clarify how the copper product will certainly respond throughout the machining process.
Proficient machinists should be experienced in translating layout specifications, picking the suitable devices, and adjusting machining criteria to reduce concerns associated with copper's one-of-a-kind machining qualities. Crossbreed machining, which integrates standard CNC machining methods with additive production, is emerging as a feasible method for creating intricate copper elements, blending the toughness of both technologies and possibly changing exactly how suppliers approach copper manufacturing.
In the realm of research study and growth, CNC machining is aiding the expedition of new copper alloys to improve efficiency further. By synthesizing copper with products such as nickel, aluminum, or tin, producers can craft compounds that have enhanced toughness, electrical performance, and resistance to put on and corrosion. These advancements can result in arising applications in sectors that depend greatly on conductive materials, such as renewable resource and electric cars. As worldwide sectors function toward higher power performance, copper's duty as a conductor in electronic circuits will stay extremely important, driving need for advanced machining options.
The aerospace and automobile markets are additionally eager adopters of copper CNC machining, particularly where lightweight elements are of important relevance. The mix of copper's light-weight nature and excellent electrical and thermal conductivity makes it a suitable selection for components such as electrical get in touches with, warmth exchangers, and wiring systems. As the shift toward electrical and hybrid lorries continues, the demand for high-performance copper components will likely surge, thus moving the requirement for sophisticated CNC machining techniques that make certain performance and quality in production. From a manufacturing perspective, the capability to introduce swiftly and supply precision-engineered components ends up being progressively necessary in dealing with the arising needs of these fast-evolving markets.
As CNC machining modern technology proceeds to establish, it enables further automation, where fundamental processes such as device adjustments, assessments, and upkeep can be configured into the production cycle. This evolution suggests that suppliers will certainly have the ability to accomplish higher productivity levels, shorter preparations, and better versatility in fitting customized requests or variants in layout. Because of this, companies that take part in CNC machining procedures are much better fit to pivot in response to the shifts in customer and market needs, promoting growth in an increasingly affordable landscape.
Discover countersink size chart exactly how copper CNC machining merges advanced modern technology with lasting practices to generate detailed, high-precision elements, driving development across sectors such as electronics, automobile, and aerospace.
The international market for CNC machining of copper is witnessing considerable growth, influenced by factors such as the increase of smart modern technologies, electric automobiles, and ongoing initiatives to enhance power efficiency throughout numerous applications. In this ability, training and evolution advancement continue to be vital; spending in workforce education and learning on CNC machining techniques, developments, and product sciences will encourage producers to remain in advance of the curve.
Finally, the integration of CNC machining with copper products offers an unique one-upmanship for suppliers in today's fast-paced industrial landscape. Its capacity to provide high accuracy, decrease manufacturing time, and enable complicated layouts makes CNC machining a crucial component of contemporary production practices. Paired with sustainability efforts, cost-effectiveness, and chances for technology, the CNC machining of copper not only satisfies the needs of contemporary applications however additionally prepares for the future trajectory of manufacturing in numerous sectors. As markets advance and the boundaries of innovation expand, embracing CNC machining's capacity will certainly be key to recognizing extraordinary growth and development in the use of copper items. The harmony of copper's material homes with innovative CNC machining strategies heralds a new age in which effectiveness, sustainability, and accuracy job together to develop revolutionary components that will define the future of manufacturing and past.